熱可塑性ポリウレタンの射出成形における課題解決事例
こんにちは!管理人のかずかずです!
皆様、いかがお過ごしでしょうか。
最近は日に日に寒さが厳しくなってきているようで、年のせいもあるのか
例年以上に寒さが骨身に染みております。
先週は大雪の影響により関越道で2000台以上の車が立ち往生するなどの
被害も出ており、今年の冬の本気度を感じる次第であります。去年は私の記憶
だとかなりの暖冬でスキー場は雪不足に喘いでいたような気がするのですが、
今年はその心配もいらなそうですね。(今年はコロナという逆境がありますが、、、)
さてさて、本題に移りたいと思います。
本日はタイトルにもあるように熱可塑性ポリウレタン(TPU)の射出成形における
課題解決の一例をご紹介したいと思います。
ポリウレタンの射出成形における課題はいくつかあるかとおもいますが、ひとつの
大きな課題として、一般樹脂に比べてはるかに柔らかい材質の為、製品取り出し時の
エジェクタピンにより突き出し部が凹んでしまうということがあります。(その分
ピンが製品を突き破って金型から取れなくなってしまうということはほとんど
ありませんが、、、)こうした不良現象を解決するために冷却時間を長くとり、
十分に固化してから取り出すためどうしてもサイクルが長くなる傾向があるのです。
実際にサイズがそれほど大きなものでなければ「成形サイクル=製品単価」のような
ものですので、成形サイクルが数秒で回せるものもあるような一般樹脂より割高に
なってしまうのはこういった特性があるためなのです。
今回ご紹介する製品の硬度はA75°と弊社取扱い材料の中でも柔らかい部類に
入る製品で、用途はある製品に組み込まれるローラーとして使われているものです。
ローラーというだけあって製品側面に余計なバリがあってはならないため、金型の
構造としては片側だけにキャビティが彫り込まれている形になります。
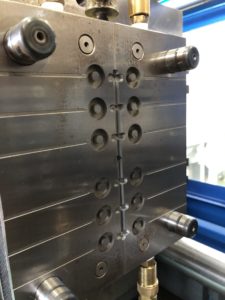
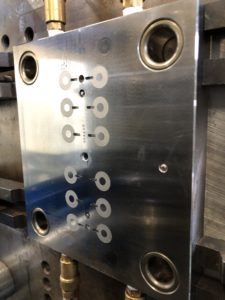
ご覧の様に固定側はシボ加工が施されているだけです。
ということはキャビティ(可動側)に製品がすべて潜り込んでいる状態に
なり、製品取り出し時にはそれなりの力が必要になるため突き出し部には
かなりの負担がかかりその部分が凹んでしまうわけです
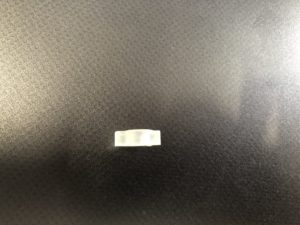
小さくて分かりづらいかもしれませんが、ポコポコと凹んでいるのがお分かり
いただけますでしょうか。もちろんこれでは製品として出荷はできません。
金型立ち上げ当初は離型剤を噴霧して対応していましたが、噴霧後数ショットは
バリが発生して捨てショットとなり、しかも10ショット程度で離型剤の効果が切れる
為、無人運転もできないので、かなり効率が悪く採算割れの製品となりかけていました。
しかし、人というのはやっているうちに考えるもので、ある方法でかなりの改善を達成
する事ができたのです。言葉で説明するよりまず動画でご覧ください。
お分かり頂けましたでしょうか。
型開き時に絶妙なバランスで固定側に引っ張られながらも、全体は
可動側に持ってこられていて、自動運転が可能になっています。
この状態で成形ができていればそもそも突き出す必要もないため
製品が凹んでしまうという事もないわけです。
どういった処理をしているかというと、何も難しいことはなく
固定側の製品部をクリーナーを付けたウエスで拭く事で、あえて
固定側に残るようにしてあげています。実際には固定側製品部のすべて
を拭いてしまうと、固定側に製品が残ってしまい、取り出し機で取れなく
なってしまうのでバランスを見ながら拭いてあげなければいけません。
また、無人で成形しているうちにどうしても可動側に強く残ってくるので
定期的に拭いてあげなければならないので、準自動運転といったところに
なるでしょうか。いずれにしても初期の効率から考えると大幅に改善している
事は確かで、現在では単価に見合った生産性で成形する事ができています。
こういった事例は、事前に流動解析を行ったり、金型側の構造で解決する
場合もあるかと思いますが、極力費用を掛けずに解決できればいいに越した事は
ありません。今回の事例の様にひとつのアイデアで大幅に改善できる事もあるわけです。
弊社では他にもオペレータの工夫ひとつで生産性向上に貢献した事例がいくつかあります。
折に触れてそういった事例もご紹介できればと思っていますが、これからも現場の力を活かし、
町工場ならではの強みを大切にしながら生産性向上、ひいてはお客様の利益に繋がる様、
努めて参りたいと思います!
最後はセールストークの様になってしまいましたので今回はこれで締めたいと思います!
それではまた!